在SMT生產工藝里面,經常會碰到經過回流焊過出來的板有錫珠,錫珠的產生,讓產品的質量沒有保證,讓外觀看起來不光滑。那產生錫珠的主要原因是什么,我們又如何去解決它,這就是我今天寫這篇文章的目的。產生錫珠的主要原因是錫膏的問題。詳細分析請看下面分析。
焊錫珠現象是表面貼裝生產中主要缺陷之一,它的直徑約為0.2-0.4mm,主要集中出現在片狀阻容元件的某一側面,不僅影響板級產品的外觀,更為嚴重的是由于印刷板上元件密集,在使用過程中它會造成短路現象,從而影響電子產品的質量。因此弄清它產生的原因,并力求對其進行*有效的控制就顯得猶為重要了。
焊錫珠產生的原因是多種因素造成的,在回流焊中的溫度時間,焊膏的印刷厚度,焊膏的組成成分,模板的制作,貼片機貼裝壓力,外界環境都會在生產過程中各個環節對焊錫珠形成產生影響。
焊錫珠是在負責制板通過回流焊爐時產生的。回流焊曲線可以分為四個階段,分別為:預熱、保溫、回流和冷卻。預熱階段的主要目的是為了使印制板和上面的表貼元件升溫到120-150度之間,這樣可以除去焊膏中易揮發的溶劑,減少對元件的熱振動。因此,在這一過程中焊膏內部會發生氣化現象,這時如果焊膏中金屬粉末之間的粘結力小于氣化產生的力,就會有少量焊膏從焊盤上流離開,有的則躲到片狀阻容元件下面,再流焊階段,溫度接近曲線的峰值時,這部分焊膏也會熔化,而后從片狀阻容元件下面擠出,形成焊錫珠,由它的形成過程可見,預熱溫度越高,預熱速度越快,就會加大氣化現象中飛濺,也就越容易形成錫珠。因此,我們可以采取較適中的預熱溫度和預熱速度來控制焊錫珠的形成。
焊膏的選用也影響著焊接質量,焊膏中金屬的含量,回流焊焊膏的氧化物含量,焊膏中金屬粉末的粒度,及焊膏在印制板上的印刷厚度都不同程度影響著焊錫珠的形成。
1:焊膏中的金屬含量:焊膏中金屬含量的質量比約為90-91%,體積比約為50%左右。當金屬含量增加時,焊膏的粘度增加,就能更有效地抵抗預熱過程中氣化產生的力。另外,金屬含量的增加,使金屬粉末排列緊密,使其有更多機會結合而不易在氣化時被吹散。金屬含量的增加也可以減小焊膏印刷后的塌落趨勢,因此不易形成焊錫珠。
.2:焊膏中氧化物的含量:焊膏中氧化物含量也影響著焊接效果,氧化物含量越高,金屬粉末熔化后結合過程中所受阻力就越大,回流焊再流焊階段,金屬粉末表面氧化物的含量還會增高,這就不利?quot;潤濕"而導致錫珠產生。
3:焊膏中金屬粉末的粒度,焊膏中的金屬粉末是極細小的球狀,直徑約為20-75um,在貼裝細間距和超細間距的元件時,宜用金屬粉末粒度較小的焊膏,約在20-45um之間,焊粒的總體表面積由于金屬粉末的縮小而大大增加。較細的粉末中氧化物含量較高,因而會使錫珠現象得到緩解。
4:焊膏在印制板上的印刷厚度:深圳回流焊焊膏的印刷厚度是生產中一個主要參數,焊膏印刷厚度通常在0.15-0.20mm之間,過厚會導致"塌落"促進錫珠的形成。在制作模板時,焊盤的大小決定著模板上印刷孔的大小,通常,我們為了避免焊膏印刷過量,將印刷孔的尺寸制造成小于相應焊盤接觸面積的10%。我們做過這樣的實踐,結果表明這會使錫珠現象有相當程度的減輕。
如果貼片機過程中貼裝壓力過大,這樣當元件壓在焊膏上時,就可能有一部分焊膏被擠在元件下面,再流焊階段,這部分焊膏熔化形成錫珠,因此,在貼裝時應選擇適當的貼裝壓力。
焊膏通常需要冷藏,但在使用前一定要使其恢復至室溫方可打開包裝使用,有時焊膏溫度過低就被打開包裝,這樣會使其表面產生水分,焊膏中的水分也會導致錫金珠形成。
另外,外界的環境也影響錫珠的形成,我們就曾經遇到過此類情況,當印制板在潮濕的庫房存放過久,在裝印制板的真空袋中發現細小的水珠,這些水分都會影響焊接效果。因此,如果有條件,在貼裝前將印制板和元器件進行高溫烘干,這樣就會有效地抑制錫珠的形成。
回流焊產生錫珠的原因及解決方案二:
焊膏與空氣接觸的時間越短越好。這是使用焊膏的基本原則。
取出一部分焊膏后,立即蓋好蓋子,特別是里面的蓋子一定要向下壓緊,將蓋子與焊膏之間空氣全部擠凈,否則幾天就可能報廢。
夏天空氣溫度大,當把焊膏從冷藏處取出時,一定要在室溫下呆4-5小時再開后蓋子。如焊膏在1-2個月短期內即可用完,建議不必冷藏,這樣可即用即開。
夏天是*容易產生錫球的季節。
由此可見,影響錫珠的形成有諸多因素,只顧調整某一項參數是遠遠不夠的。我們需要在生產過程中研究如何能控制各項因素,從而使焊接達到*好的效果。
通過上面的詳細分析,我們可以總結出來:錫珠主要跟:錫膏質量,印刷厚度,貼片機貼裝壓力,與空氣接觸時間長短等重要因素有關。要解決這個問題,就要改善以上這些問題,這樣你的產品才不會才生錫珠,讓你的產品更有保障!
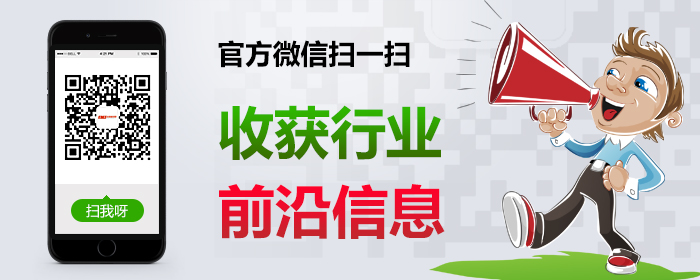